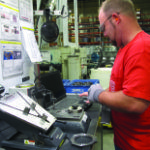
A group of manufacturers from APEG’s southern counties got a close look at how continuous improvement processes can save a company money and improve productivity.
APEG-MEP’s first Lean Networking Tour was hosted by GKN Sinter Metals, Gallipolis, in December and was attended by 21 manufacturers from 8 companies.
“Manufacturers want to know how things work and we decided the best way to understand continuous improvement processes was to see how they operate in a lean culture like GKN,” said Bryan Smith, MEP account executive. GKN has used lean processes for 14 years.
The three-hour visit included networking time, an introduction by Anthony Dicken, plant manager, and a 50-minute small-group tour of the facility. It wrapped up with a 45-minute Q&A and discussion.
The tour highlighted four of GKN’s key areas of lean manufacturing.
- Continuous Improvement – Preventive maintenance
- Quality Control – Shop floor management
- Process Improvement – Touch screen training resource board
- Lean Manufacturing – FIFO (First-in-first-out) lanes for forge
“When the tour was finished we gathered positive observations from the attendees, going around the room several times until they were all shared,” said Smith, “then we asked for improvement opportunities they saw on the tour. Gathering this kind of information is also part of continuous improvement.”
APEG-MEP is one of six Ohio Manufacturing Extension Partnership affiliates which is part of a national program designed to grow and increase the competitiveness of American manufacturing.
If you would like information about hosting or attending the next Lean Networking Tour contact Bryan Smith at 740.821.2441 or bsmith@apeg.com.